PRODUCTS
CONTACT US
Ningbo Nide International Co., Ltd.
一一
· Contact person:Jack Zeng
· Mob/Whatspp/WeChat:0086-13738869026
· Email:emarketing@nide-group.com;marketing4@nide-group.com
· Add:No. 169, Wohushan Road, Daqi Subdistrict, Beilun District, Ningbo, China
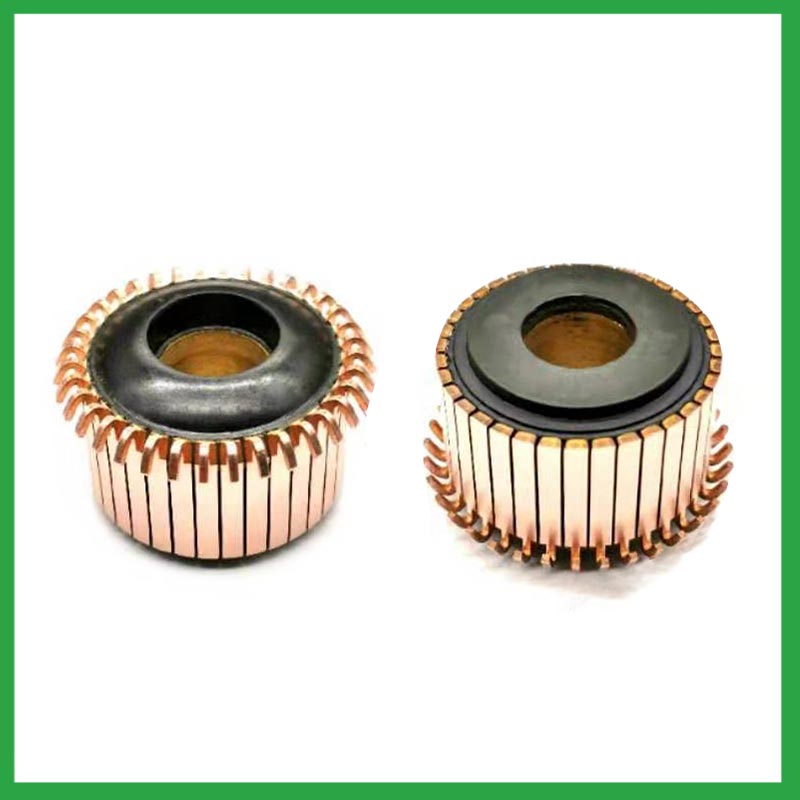
Model:NDPJ-HXQ-1006
The 36P hook commutator is suitable for drum washing machine motor.
Categoryes: Commutator
Product Name : | 36 segment Commutator for washing machine DC Motor |
Color : | Copper Tone |
Material : | Copper, Steel; 0.03% Or 0.08% Silver Copper |
Type : | Hook commutator |
Tooth Quantity : | 36 Pcs |
Usage: | DC MOTOR |
Size: | Customized |
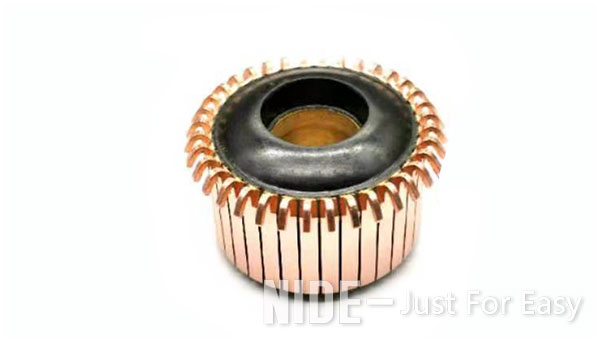
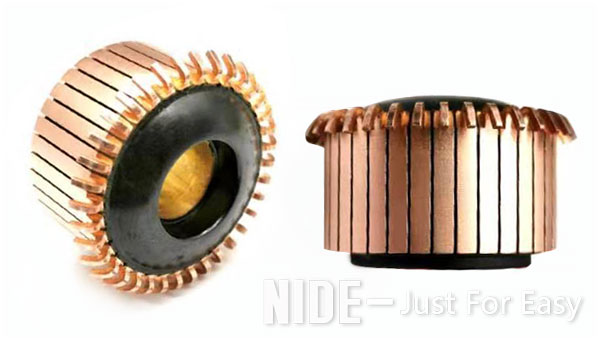
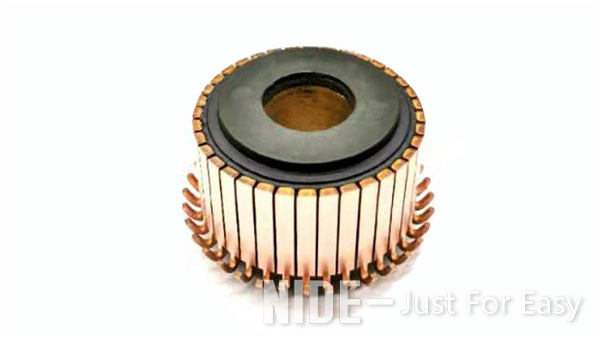
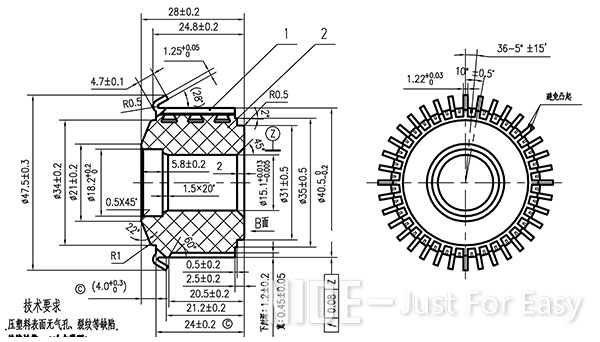
Information needed for commutator inquiry:
It will be better if customer could send us detailed drawing including below information.
1. Commutator dimension: OD, ID, total height, and copper height, bar number.
2. Commutator type: hook type, raiser type or planner
3. Copper material: Agcu/ Cu
4. Commutator applications
5. Required quantity
6. Copper bush needed or not
7. Other technical requirement.
If possible, it will better if customer could send us samples.
Nide produces more than 1200 different types of motor commutator, including hook type, riser type, shell type, planar type, ranging from OD 4mm to OD 150mm and we are professional in manufacturing commutator for many years. The commutators are widely applied to automotive industry, power tools, household appliances, and other motors.If our existing models are not suitable for you, we could also develop new tooling according to your drawing and samples.
Besides, we can supply the full range of motor components such as commutator, ball bearing, thermal protector, carbon brush, insulation paper material, shaft, magnet, fan, motor cover,etc.
Tags: Commutator
What is the Function of a Segment Hook Commutator in Electric Motors, and How Does it Contribute to Smooth Operation?
The segment hook commutator in electric motors plays a significant role in converting electrical energy into mechanical motion. A commutator is a component of the rotor, especially in DC motors. Nide International believes that it has these main functions:
Current reversal: The segment hook commutator reverses the direction of current in the motor coil winding. When the rotor rotates, the commutator ensures that the current in the coil changes direction at the appropriate time, which is crucial for maintaining a consistent direction of rotation.
Continuous rotation: By reversing the direction of current in the coil winding, the commutator allows the rotor to rotate continuously. Ensure that the magnetic force between the rotor and stator remains in a repulsive state, promoting smooth and continuous rotation of the motor.
Preventing Armature Reaction: The commutator helps to counteract the negative effects of armature reaction, as the magnetic field generated by armature current can affect the motion of the rotor. The commutation process minimizes armature reaction to ensure the stability of motor operation.
Maintaining torque: Commutation is crucial for maintaining a constant torque in the motor. The segment hook commutator ensures stable and efficient operation of the torque generated by the motor by controlling the direction of the current.
Reducing electrical noise: A normally functioning commutator helps to reduce the electrical noise generated during motor operation. Smooth commutation helps to minimize sparks and arcs at the brushes, resulting in quieter and more reliable motor performance.
What Factors Influence the Design and Material Selection for Segment Hook Commutators in Different Motor Applications?
In different motor applications, the design and material selection of segment hook commutators are influenced by these factors to ensure optimal performance, durability, and efficiency.
1. The specific type of motor and its expected application play a crucial role in the design of commutators. Different types of motors, such as DC motors, general-purpose motors, or brushless AC motors, may have different requirements for inverter design based on factors such as speed, torque, and duty cycle.
2. The rated power of the motor determines the electrical and mechanical stresses that the commutator will withstand. Higher rated power may require more robust materials and designs to handle increased current and mechanical loads.
3. The speed of the motor affects the design of the commutator. High speed applications may require special consideration to minimize wear, friction, and potential sparks.
4. The current carrying capacity and voltage requirements of the motor affect the design of the commutator. Materials with high conductivity and insulation performance can be selected based on these factors.
5. The operating environment, including temperature, humidity, and the presence of pollutants, can affect the selection of materials. Corrosion resistance, thermal stability, and environmental sealing may be key considerations.
6. Due to the sliding effect of the electric brush, the commutator is prone to wear and tear. Wear resistance is a key factor, and materials with good wear resistance, such as certain metal alloys, can be selected.
7. Minimizing the friction between the commutator and the brush is crucial for efficiency and lifespan. The selection of materials and the application of lubrication or coatings can affect the level of friction.
8. The size and geometric shape of the commutator are customized according to the motor design and mechanical requirements. Commutators can have different shapes, such as segment hook designs, to adapt to specific motor configurations.
9. The cost of materials and manufacturing processes is a practical consideration. Balancing performance requirements and cost-effectiveness is crucial for commercial feasibility.
The commonly used materials for commutators include copper and its alloys, which have good conductivity and wear resistance. Silver has excellent conductivity and is often used in high-performance applications. In some cases, materials such as mica can be used as insulation components within commutators.
How Does the Maintenance and Inspection of Segment Hook Commutators Impact the Overall Performance and Lifespan of Electric Motors?
The regular maintenance and inspection of the segment hook commutator plays an important role in the overall performance and extended service life of the motor.
Through daily inspections, resolving wear issues and promptly addressing potential issues, maintenance helps optimize motor efficiency. Inspection includes evaluating the condition of the brushes, ensuring proper alignment, and detecting signs of sparks or uneven wear on the commutator blades.
Cleaning and lubrication during maintenance can prevent excessive friction, reduce wear and heat accumulation. Timely replacement of worn brushes and damaged segments helps maintain consistent contact and effective commutation, thereby maintaining motor performance.
Taking appropriate maintenance measures to address issues such as arcing may lead to increased electrical noise and reduced efficiency.
Overall, a well maintained and regularly inspected segment hook commutator ensures reliable motor operation, minimizes downtime, and extends motor life in various applications.